CAM Follower Mechanism 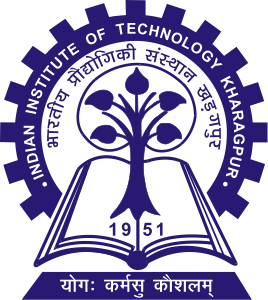
Introduction
A cam is a rotating machine element which gives reciprocating or oscillating motion to another element known as follower. The cam and the follower have a line contact and constitute a higher pair. The cams are usually rotated at uniform speed by a shaft, but the follower motion is predetermined and will be according to the shape of the cam. The cam and follower is one of the simplest as well as one of the most important mechanisms found in modern machinery today. The cams are widely used for operating the inlet and exhaust valves of internal combustion engines, automatic attachment of machineries, paper cutting machines, spinning and weaving textile machineries, feed mechanism of automatic lathes etc.
Theory
Cams are mechanical devices which are used to generate curvilinear or irregular motion of mechanical elements. They are used to convert rotary motion into oscillatory motion or oscillatory motion into rotary motion.Necessary elements of a cam mechanism are:
- A driver member known as the cam
- A driven member called the follower
- A frame which supports the cam and guides the follower
Classification of Followers
- According to the surface in contact:
The followers, according to the surface in contact, are as follows :
(a) Knife edge follower:
When the contacting end of the follower has a sharp knife edge, it is called a knife edge follower, as shown in Fig. 2(a). The sliding motion takes place between the contacting surfaces (i.e. the knife edge and the cam surface). It is seldom used in practice because the small area of contacting surface results in excessive wear. In knife edge followers, a considerable side thrust exists between the follower and the guide.
(b) Roller follower:
When the contacting end of the follower is a roller, it is called a roller follower, as shown in Fig. 2 (b). Since the rolling motion takes place between the contacting surfaces (i.e. the roller and the cam), therefore the rate of wear is greatly reduced. In roller followers also the side thrust exists between the follower and the guide. The roller followers are extensively used where more space is available such as in stationary gas and oil engines and aircraft engines.
(c) Flat faced or mushroom follower:
When the contacting end of the follower is a perfectly flat face, it is called a flat-faced follower, as shown in Fig. 2 (c). It may be noted that the side thrust between the follower and the guide is much reduced in case of flat faced followers. The only side thrust is due to friction between the contact surfaces of the follower and the cam. The relative motion between these surfaces is largely of sliding nature but wear may be reduced by off-setting the axis of the follower, as shown in Fig. 2 (f ) so that when the cam rotates, the follower also rotates about its own axis. The flat faced followers are generally used where space is limited such as in cams which operate the valves of automobile engines.
(d) Spherical faced follower:
When the contacting end of the follower is of spherical shape, it is called a spherical faced follower, as shown in Fig. 2 (d). It may be noted that when a flat-faced follower is used in automobile engines, high surface stresses are produced. In order to minimise these stresses, the flat end of the follower is machined to a spherical shape.
- According to the path of motion of the follower
The followers, according to its path of motion, are of the following two types:
(a) Radial follower
When the motion of the follower is along an axis passing through the centre of the cam, it is known as radial follower. The followers, as shown in Fig. 2 (a) to (e), are all radial followers
(b) Off-set follower
When the motion of the follower is along an axis away from the axis of the cam centre, it is called off-set follower. The follower, as shown in Fig. 2 ( f ), is an off-set follower.
Fig. 2. Classification of followers.
Terms Used in Radial Cams:
Fig. 3 shows a radial cam with reciprocating roller follower. The following terms are important in order to draw the cam profile
Base circle.
It is the smallest circle that can be drawn to the cam profile.
Trace point.
It is a reference point on the follower and is used to generate the pitch curve. In case of knife edge follower, the knife edge represents the trace point and the pitch curve corresponds to the cam profile. In a roller follower, the centre of the roller represents the trace point.
Pressure angle.
It is the angle between the direction of the follower motion and a normal to the pitch curve. This angle is very important in designing a cam profile. If the pressure angle is too large, a reciprocating follower will jam in its bearings.
Pitch point.
It is a point on the pitch curve having the maximum pressure angle.
Pitch circle.
It is a circle drawn from the centre of the cam through the pitch points.
Pitch curve.
It is the curve generated by the trace point as the follower moves relative to the cam. For a knife edge follower, the pitch curve and the cam profile are same whereas for a roller follower, they are separated by the radius of the roller.
Prime circle.
It is the smallest circle that can be drawn from the centre of the cam and tangent to the pitch curve. For a knife edge and a flat face follower, the prime circle and the base circle are identical. For a roller follower, the prime circle is larger than the base circle by the radius of the roller.
Lift or stroke.
It is the maximum travel of the follower from its lowest position to the topmost position.
Fig. 3. Terms used in radial cams.